- Obituary – Mr E J C Smith
- Sharpening our International Competitive Edge
- Steloy Stainless Precision Castings a new Hi-Tech Foundry
- New Afrox Electrode meets standards for Large Export Order
- How Important is the Stainless Steel Industry?
- Stainless Steel Elution Column for Nigel Gold recovery plant
- BMW’s “GREAT” Stainless Logo
- “Stainless Steel For All Seasons”
- SA Cryogenic Vessels Grab Share of World Market
- View Increased Sales for Coloured Stainless Steel
- “Think Bank” Programme
- Consani Tanks Penetrate World Markets
- Stainless Sparkles in Beer Keg Battle
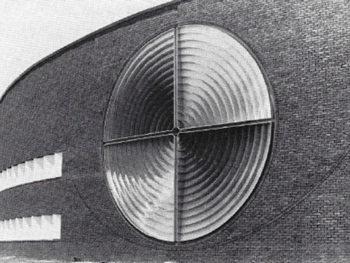
The “Great” BMW logo which can be seen by the ‘passing parade’ from the Ben Schoeman highway epitomizes the excitement and versatility STAINLESS STEEL can create.
An interesting stainless steel project was recently completed by Architectural Aluminium (Pty) Ltd (ARCUM) for Midrand Project Management Services. The project involved supplying and erecting on site a 9 metre diameter circular BMW logo which was designed by Architects Hallen Theron and Partners. The consulting structural engineers were Messrs Hill Kaplan Scott Inc and the quantity surveyors, Messrs Schoombie, Hartman and partners.
Paul Custers of Hallen Theron had this to say about the logo: ‘The building and the logo had to serve as a statement of BMW’s commitment to South Africa and had to emulate the style and quality that goes into manufacturing BMW motor cars. In the early days BMW were involved in making aeroplane engines and our idea for this “Great Logo” originated from the image one gets when a propeller turns.’
The basic structure had to be strong enough to withstand both Positive and Negative windloads due to the circular shape of the building and a convex wall. Therefore the choice of materials was important and the final decision to use STAINLESS STEEL for the fins contributed largely to the structural and visual authenticity of the distinctive logo. The logo had to look ‘alive’ and the movement and visual tricks were achieved by using two different finishes on the stainless steel fins. The effect was heightened by the varying depths of the quadrants – two fins in the ‘Satin Finish’ recessed 700mm, opposite two shallow, highly polished fins. Shorter lengths of stainless steel were used to overcome the problem of cutting the fins which were hand-rolled and fitted on site by ARCUM.
The innovative manufacturing skills of ARCUM, The Professional Team and Kool Aluminium rose to the challenge and combined constructively to convert a concept into a conclusion to the satisfaction of the client.