- Vacuum Insulated CO 2 Tanker
- 3CR12 – Southern Cross Steel
- Senior appointments at Jacksons
- Turbine Integral Steam Piping and Fittings for Koeberg
- Market Intelligence
- R8,5 Million Investment By Jacksons
- Manufacture of centrifugally cast tube in South Africa
- Aloe plant moves to Alrode
- Sassda AGM
- Jacksons in Zimbabwe
- Growth of Alloyfab
- Rodney Ranger at Jacksons
- NDE move into stockholding
- Awards from S.A.I.W.
- The South African Market
- Case History on 3CR12 intermediate chute liners
- The Development of a Chromium – containing corrosion resisting steel
Metallurgical Processes (Pty) Ltd was founded more than 15 years ago and in 1970 the company was acquired by Impala Platinum Ltd. (A Union Corporation Company), which markets refined nickel as a by-product of its platinum group metals interest.
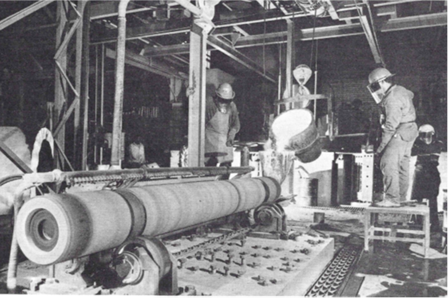
Tube casting at Metallurgical Processes, showing one of the machines with the cover removed
Metallurgical Processes specialise in the production of high quality nickel base master alloys for the foundry industry and is recognised internationally as one of the leading manufacturers of special high nickel alloys and nickel magnesium which is used in the production of ductile cast iron.
Centrifugal Casting
The centrifugal casting facility was developed through technical license agreement with one of the world’s foremost producers, Pose Marre Edelstahlwerk of West Germany.
In this process, molten metal from an electric arc furnace is poured into a rapidly rotating cylindrical mould. The centrifugal force of the rotating mould is about 100 times greater than gravity and causes the molten metal to spread evenly over the full length of the inner mould surface forming a tube with a uniform wall thickness and a dense and sound structure. By contrast, in static castings the filling of mould is under gravity alone and does not have the same mechanical properties.
Metallurgical Processes produce centrifugally cast tube in a variety of alloys and special emphasis is placed on the production of high nickel alloys and stainless steels.
Some typical examples of alloys which are available to international specifications are listed:
Austenitic stainless steels
Ferritic stainless steels
Martensitic stainless steels
High nickel-base alloys
Cupro nickel alloys
Nickel-copper alloys
Nickel-chrome-iron heat resisting alloys
The tube casting equipment is capable of producing tubes of up to 5 500 mm in length and up to 650 mm in outside diameter.
The centrifugal casting process imposes limitations on a minimal wall thickness for pressure soundness at about 8 mm (before machining), and on a minimum outside diameter of about 75 mm.
During initial development of the centri-cast operations, facilities were not available to achieve the mandatory pull-boring requirements for specific petro-chemical furnace tubes. Accordingly Metallurgical Processes have installed a pull-boring facility at their works site under the auspices of a subsidiary engineering company. This facility has the capacity to bore tube lengths of up to 5 200 mm.
Metallurgical Processes will undertake the fabrication of complete units such as reformer tubes, furnace rolls, and radiant heater banks.
Full technical advice is also available as well as a comprehensive range of testing facilities including X-Ray fluorescence, tensile tests, metallography, pressure testing and the provision of analysis certificates.