- Making Stainless Even Better
- Sassda News
- New Alloy to Combat Cost of Nickel
- A Brighter Future For Stainless
- Markedly Different Trading Environment
- Czech-Mate
- Building the Use of Stainless
- New Stainless Project
- Latest on SSCDI Activities
- The Currency of the Future
- New Autocat Factory
- Partnering Alliances Froth Up Market
- Stainless for Millennium Bridge
- South Africa’s Stainless Sector Shines Bright
- Sector Fails to Steel Itself for E-Commerce
- Stainless in Space
- Using Stainless for LPG Cylinders is a Gas
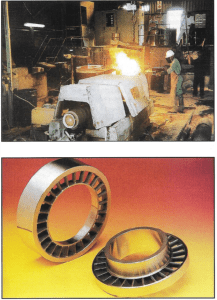
The spin-casting facility at Chamdor (top), and an example of modern casting products (bottom)
Rely Precision Castings, one of the largest stainless foundries in the southern hemisphere, has developed a new alloy for a specific application for continuous-cast rolls at Iscor. Stainless Steel casts a closer look at the breakthrough, and the role of alloys in general.
The term ‘stainless’ is used to describe a large family of corrosion-resistant alloys. These all contain a minimum percentage by weight of 10% chromium, and are grouped according to their crystal structures. Ferritic grades, commonly known as cutlery grades, contain Cr in the range of 10% to 26%. However, these alloys display poor weldability, and generally only thin sections can be welded. These grades also suffer from rampant grain growth when exposed to elevated temperatures.
Austenitic grades are alloys containing about 17% Cr and 10% Ni to produce a fully austenitic microstructure. These alloys exhibit excellent corrosion resistance, and in some cases molybdenum is added to enhance this characteristic even further. The weldability of these alloys is good, and can be improved if the carbon levels are kept low. Although this is the most widely used group of stainless, they have relatively low strengths and high ductility, but are susceptible to stress-corrosion cracking.
The microstructure of duplex grade alloys comprise a combination of austenite and ferrite, usually in the ratio 50:50. The Cr content varies between 18% to 26%, while the nickel content averages between 4% to 26,5%. Corrosion resistance is also improved by the addition of molybdenum. These alloys are weldable, have higher strength than austenitic grades, and are much more resistant to stress-corrosion cracking.
Properties can be modified
The properties of all these grades can be modified to enhance specific properties by additional alloying with Ti, Nb, Ta, Cu, C, si, Mn, Al and S [sic]. Various attempts have also been made to produce duplex stainless steels in which the nickel content has been reduced due to the cost of nickel. Since July 1999, the cost of nickel shot from R34,64/kg to R76,52/kg in May last year.
André van Bennekom, in conjunction with Rely, developed the new stainless alloy with a duplex microstructure, known as Relinite. It has a nickel content below 1% by mass, a nitrogen content between 0,10% to 0,35% and a manganese content between 3% to 10%. The austenite content of the alloy is preferably 50% by volume or greater so as to ensure that the nitrogen solubility limit for the alloy is not exceeded. Another feature of the alloy is that the austenite may also be transformed to martensite during cold deformation, a phenomenon commonly known as work hardening. This property can only be achieved by limiting the nickel to below 1%.
In order to improve the corrosion resistance, the Cr content of the alloy is kept below that usually specified for duplex stainless steels. The Mn addition provides the alloy with the required nitrogen solubility so as to promote the austenite microstructure at the recommended nickel level. As in normal stainless steels, molybdenum may be added to increase corrosion resistance. “Modern steel technology has produced a material that offers exceptional qualities of corrosion-resistance, heat-resistance, strength, ease of casting and impact resistance, as well as being aesthetically-pleasing and hygienic to work with,” says Ian Gibson of Rely.
Modern foundry technology
“In addition, modern foundry technology can offer designers and specifiers numerous advantageous options. In engineering applications, castings permits greater freedom of structural design, and allows significant savings in materials when compared with fabrication. There are no welded joint weaknesses, and uniformity of structure and reduced distortion due to there being no weld beads or heat-affected zones.”