Stainless steel is critical in our food, beverages and pharmaceutical consumer products processes due to its hygienic properties
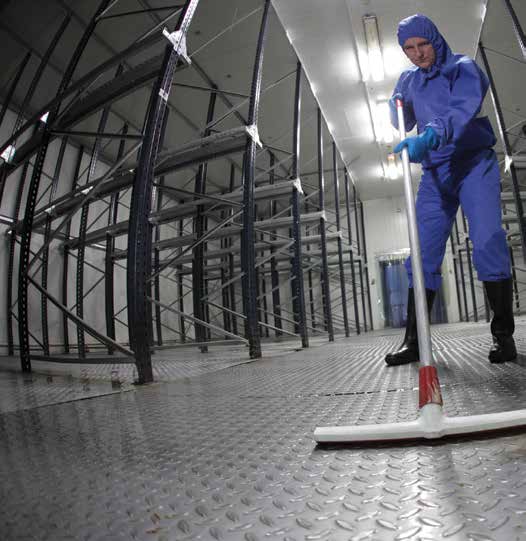
Stainless steel is used in a variety of industries that require hygiene control as it can withstand extreme cleaning techniques. It also does not corrode or leach toxic by-products
Globally regulators and lawmakers are increasingly concerned with the potential impact of materials and products on human health and the environment.
Such concerns tend to be reinforced in the minds of the regulators by adverse news items carried in the media, which is reflected by public unease about food safety, health and environmental issues.
It is common knowledge that stainless steel is selected in industry mainly for its resistance to corrosion. However, this is not the only reason for selecting stainless steel. Other criteria such as aesthetic appearance; high and cryogenic temperature performance, as well as life cycle costing are also important when stainless steels are selected for a specific application.
End-users tend to neglect how stainless steels touch our daily lives, especially when it relates to our health.
Stainless steel is critical in the processes through which our food, beverages and pharmaceutical consumer products are prepared, packaged and delivered. Our lives often depend on stainless steel when receiving medical attention and once we die, our bodies are preserved on stainless steel surfaces at the morgue.
The reason for this is the high levels of hygiene that stainless steel offers.
Stainless steel remains one of the most hygienic industrial materials known and this attribute can be explained by the same phenomena that delivers its high corrosion resistance: the passive layer.
THE PASSIVE LAYER
The key to stainless steel’s corrosion resistant characteristic is the passive layer that forms on the material surface once there is more than 11% of chromium in the alloy. Once this level has been achieved, a thin chromium oxide layer will develop when the chromium reacts with the oxygen in the surrounding environment. This layer, unlike iron oxide or rust, is inactive or inert. This means that the surface layer becomes “unwilling” to react with other chemical elements it comes in contact with, thus it’s corrosion resistant properties. For the same reason stainless steels are regarded as highly hygienic compared to other materials.
APPLICATIONS
Materials potentially suitable for these applications must meet the following requirements :
- durability,
- adequate mechanical and physical properties,
- ease of fabrication and
- inert surfaces that can be easily cleaned and offer high levels of hygiene.
The stainless steel family offers solutions to all of these requirements. In this discussion the focus will be on the following applications:
- Food and beverage applications
- Drinking water supply
- Medical applications
- Pharmaceutical plant and process applications
FOOD & BEVERAGE APPLICATIONS
Materials used for the preparation, processing and storage of food and beverage products are not only required to maintain the integrity of the structure, i.e. it should have the correct range of mechanical and physical properties for a good structural design. It should also be able to resist chemical activity of the surface with the foodstuff or beverage that it is in contact with. It is required that surfaces in this application be sufficiently inert to impart neither colour nor flavour to product.
Stainless steels are selected for this application, because they are resistant to corrosion, inert, easily cleaned and sterilized without loss of properties.
In the majority of food contact applications where stainless steel is used, austenitic grades with 18% chromium provide an optimum balance of corrosion resistance, cost and ease of fabrication.
Grade 304 is used in relatively mild environments (with a chloride content less than 250 mg/l) for both domestic and professional cutlery, hollowware, and kitchen utensils. It is used to a lesser degree for process and storage vessels.
Grade 316 is suitable for more aggressive service environments with chloride contents up to 500 mg/l.
For this reason, austenitic grades with molybdenum contents are used in critical areas. Nevertheless, ferritic, martensitic and duplex stainless steels are also used in food and beverage applications.
Stainless steels in contact with foodstuffs have been subject to a number of studies. In some of these studies, the release of nickel from stainless steel saucepans was evaluated for a variety of foodstuffs and water.
The studies revealed that, on first use, measurable levels of nickel were detected.
It was also shown that, as the number of subsequent uses increased, the level of nickel release diminished and reached a steady state. In all cases, release of chromium, molybdenum and nickel were all well below the Council of Europe’s specific release limits. These observations reflect the changes that occur in the passive oxide layer on first immersion of stainless steels in aqueous media.
DRINKING WATER SUPPLY APPLICATIONS
Materials for drinking water supply equipment must be corrosion resistant to both internal and external service environments and sufficiently robust to withstand the forces generated in these applications. The longevity of these materials is an additional and important factor in their selection, especially as many water supply pipes and other items of equipment are buried below ground. It would therefore makes sense to include a life cycle costing as part of the evaluation process for material selection. For such applications, life span requirements often ask for a design life in excess of 100 years.
Drinking water regulations are designed to ensure that surfaces in contact with drinking water impart neither colour, odour nor flavour and prevent consumers from exceeding the maximum Stainless steels are widely used in drinking water supply systems, because they are resistant to corrosion, inert and can be readily fabricated by a variety of techniques. The selection of an appropriate stainless steel grade for drinking water applications depends on the composition of the drinking water (the internal environment) and the external service environment. For this reason, it is difficult to provide a list of stainless steel grades used for specific applications, but it would require an analysis of all factors impacting on both the internal and external environment. Grade 316 is recommended for atmospheric exposure in areas of significant industrial pollution and/or coastal regions or in subterranean applications with acid and/or high chloride soils. In some cases, the duplex stainless steels grades 2205 and 2304 may
be necessary.
Due to the importance of ensuring quality of drinking water, stainless steels in contact with drinking water have been subject to extensive studies.
These studies demonstrate that, under normal operating conditions, the release of chromium and nickel from stainless steels is at, or below, the limits of detection for current analytical techniques (i.e. 1-2 parts per billion).
MEDICAL APPLICATIONS
Medical devices must possess appropriate mechanical and physical properties to meet their design criteria. In addition, they must exhibit adequate corrosion resistance when exposed to body fluids, cleaning agents and disinfectants as well as withstanding a variety of sterilising techniques and remain passive and hygienic.
Although stainless steels have long been used in medical device applications, it is important to distinguish between stainless steels used for implant applications and commercial grades used for other medical devices such as dental equipment and surgical forceps, kidney dishes, theatre tables, etc.
Regulations define implants as medical devices that are exposed to human tissue for more than 30 days and will usually be made from highly specialised materials and grades of stainless steel and titanium.
Once again, the final choice of grade will be dependent on many in-service factors. Stainless steel grades used for surgical and dental instruments are specified by the ISO 7153-15 standard. In ISO 7153-1 the grades of stainless steel specified are generic and represent typical and readily available grades indicating that stainless steels are not specifically prepared for surgical applications. This standard also provides an indication of typical applications for each grade.
Martensitic stainless steel is used extensively for dental and surgical instruments, the reason being that these stainless steels can be hardened and tempered by heat treatment. This process allows the development of a wide range of mechanical properties. It can be given a high hardness for cutting instruments or a lower hardness with increased toughness for load-bearing applications.
Austenitic stainless grades are also used for medical devices. Grade 303 stainless steel is used where its free machining properties enhance the ease of manufacture of medical devices with screw threads, with drilled and tapped holes. Handles of multi-part dental instruments are often also manufactured in this grade, because its lower corrosion resistance is not a disadvantage in this case. Grade 304 is used when good corrosion resistance and moderate strength is required, for example, in the manufacture of dental impression trays, hollowware, retractors, guide pins, theatre tables and storage cabinets, while grade 316 are used for dental explorers and vaginal probes.
Wrought stainless steel and highnitrogen stainless steel, respectively, for surgical implants, is specified in ISO standards 5832-16 and 5832-97.
The original development of these materials was based on grade 316. Implant grade stainless steels have specific requirements for pitting corrosion resistance and hygiene that cannot be attained through the same processes as that for commercial grades.
Therefore special production routes are used to produce so called “clean” implant steels. These activities will include vacuum melting or electro-slag re-melting.
The regulatory concerns for implants concerns bio-compatibility, control of biological contamination and free from residual production debris.
Implants are therefore subject to very specific surface finish requirements. The surfaces are often mechanically polished to a high finish followed by electro-polishing. This enhances the corrosion resistance and improves fatigue life. Electro-polished finishes render a chemically clean, smooth surface.
Implants are also subject to stringent cleaning regimes in order to remove microbiological contamination, which could add risk to the patient.
Leaching of metal compounds when in contact with body tissue and fluids remain a debatable issue, which concerned medical staff when their patients have exhibited allergies attributable to specific metals such as nickel.
PHARMACEUTICAL PLANT AND EQUIPMENT APPLICATIONS
As with the food and beverage industry, pharmaceutical applications also demand that the materials of construction be corrosion resistant and sufficiently robust to withstand the service environment. Once again, inert surfaces are required to minimise the risk of any chemical leaching or chemical reaction with the product. Stainless steel is widely used in the pharmaceuticals industry, because of its corrosion resistance and inert surfaces which are easily cleaned, and the added advantage of ease of fabrication.
Grade 316 is the most widely used stainless steel in pharmaceutical plant and is considered globally as the industry standard. However, materials for each application are selected on the Medical equipment must be able to withstand sterilising techniques and still remain hygienic basis of their resistance to corrosion in a specific service environment. The selection of a suitable grade of stainless steel will include consideration of the cleaning regime and chemicals to be used.
The operational process of the plant will indicate whether continuous with a “clean in place” (CIP) system or batch operation with shutdowns to clean the plant is employed. This will also influence the choice of material.
The austenitic stainless steel grade 304 is used in mild corrosive environments with chloride content lower than 250 mg/l, whilst grade 316 is to be used with chloride levels up to 500 mg/l.
At higher chloride levels, especially when combined with increased operating temperatures, the duplex stainless steel grades such as 2205 and 2304 should be considered for its resistance to stress corrosion- cracking.
CLEANABILITY
It has been shown in the preceding sections that stainless steel has the mechanical and physical properties combined with superior corrosion resistance to be suitable for all the applications as discussed.
Although corrosion resistance plays a critical role in so-called hygienic surfaces, the true test lies in cleanability, not only to ensure cleanliness from remnants, debris and other possible contaminants, but also to act as an effective barrier to bacteriological contamination.
When considering the cleanability of stainless steel compared with other materials such as plastics and porcelain, stainless steel fares best.
Stainless steel is virtually completely free of bacteriological retention after one wash. It is worth noting that natural wood has got better performance than plastics when combating bacteriological contamination. Natural bacteria and enzymes in untreated wood actively attack and destroy contaminants from biological sources.
CONCLUSION
Stainless steel provides suitable solutions for industrial and personal hygiene requirements. It has the mechanical and physical properties to comply with structural and engineering demands and provides a safe and healthy environment where delicate and sensitive products can be produced, packaged and stored. The highly corrosive resistant nature of stainless steel gives it an added advantage of no requirement for surface coatings and ease of cleaning and maintenance. As such stainless steel is the preferred material for cost-effective and highly functional components and equipment in any environment with hygiene requirements.